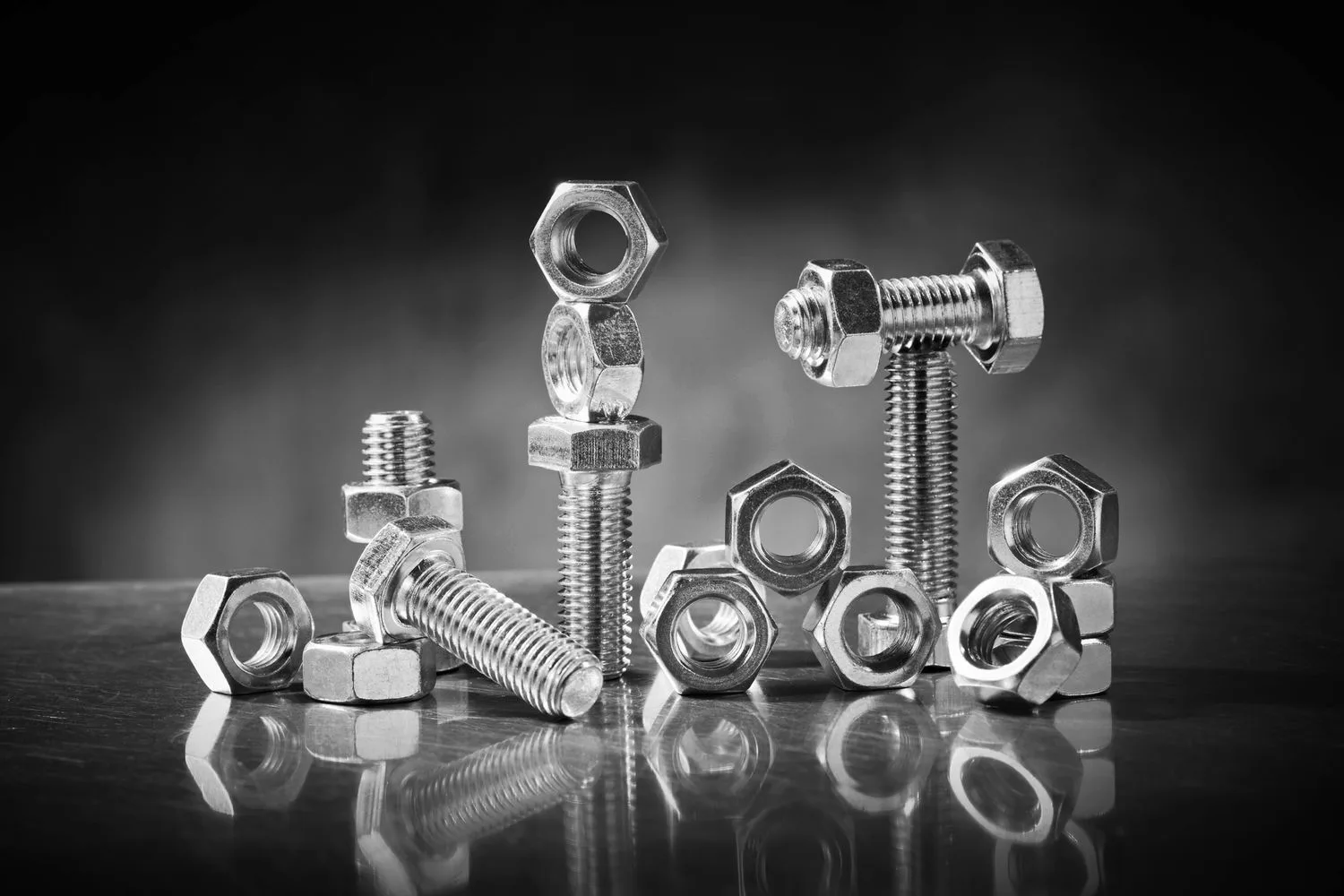
What is a Bolt? Types of Bolts and Their Applications
Bolts are essential fasteners used in various industries, including construction, automotive, and machinery manufacturing, ensuring the secure and sturdy connection of two or more components. With their historical development, diverse material options, manufacturing techniques, and applications, they have become indispensable in engineering. In this article, we will thoroughly explore the definition of bolts, their applications, manufacturing processes, types, the differences between stainless and standard bolts, and special head bolt varieties.
Definition of a Bolt
Bolt is a fastening element designed to join two or more parts together, typically featuring a cylindrical body covered with helical threads. This element is one of the most commonly used members of the fastening family. The structure of a bolt consists of three main parts: the head, the body, and the threaded section. The head can come in various shapes (hexagonal, Allen, round, etc.) and is designed to provide the required clamping force for the application. The body determines the load-bearing capacity, while the thread structure ensures compatibility with nuts or other fastening elements.
These components play a critical role in ensuring the integrity of mechanical connections. A bolt can maintain a secure connection even under high torque applications. Particularly in heavy industry applications, it provides a reliable connection due to its resistance to vibrations and sudden load changes. Moreover, bolts have evolved over time; they have been produced in different types (e.g., automotive bolts, construction bolts, aerospace bolts) to meet industrial needs and technological advancements. Each type has specific application areas and advantages.
Types of Bolts
Bolts are among the most commonly used components in fastening elements. There are many different types of bolts used across various industries. Here are the most commonly used bolt types:
1. Allen Bolts
Allen bolts are special fastening elements with a hexagonal socket that are tightened using an Allen key. They provide strong fastening in small and tight spaces.
2. Stainless Steel Bolts (Inox Bolt, Chrome Bolt)
Stainless steel bolts are preferred especially in outdoor applications exposed to water and moisture. Also known as inox bolts and chrome bolts, these types are highly resistant to corrosion.
3. Countersunk Head Bolts
Countersunk head bolts are designed to sit flush with the surface. They are commonly used in furniture and metalworking. They are preferred for their aesthetic appearance.
4. Standard Bolts
Standard bolts are general-purpose fastening elements and are the most widely used. They are typically hexagonal or star-headed.
5. Hex Socket Head Bolts (Allen Bolts)
Hex socket head bolts, also known as Allen bolts, provide a strong connection due to their hexagonal socket. They are preferred in applications requiring high strength.
6. Hex Head Bolts
Hex head bolts are among the most commonly used industrial fastening elements. They can be easily tightened with a wrench or socket tool.
7. Flat Head Bolts
Flat head bolts are usually used in applications where they sit flush with the surface and are often chosen for decorative purposes. They minimize visibility in assembly operations.
8. Flanged Bolts
Flanged bolts have an integrated washer at the head, providing a larger surface area for a more secure connection.
9. Double Threaded Bolts, Large Threaded Bolts
Double threaded bolts are special bolts commonly used in heavy industry applications requiring high strength connections. Large threaded bolts have a wider thread pitch and are typically designed for vibration-resistant connections.
10. Other Special Bolt Types
Many specialized bolt types are designed for unique applications. Some of these include:
- Set screws – Used to secure moving parts.
- Brass bolts – Preferred in the electronics industry due to their electrical conductivity.
- Eye bolts – Used in hanging and fastening applications thanks to their hooked design.
Choosing the right bolt according to industry and application needs enhances the safety and durability of the connection.
Important Factors When Choosing a Bolt
Bolt selection is crucial for ensuring the strength and longevity of a connection. If the correct bolt is not chosen, loosening, corrosion, or mechanical failures may occur at the connection points. Here are the most important criteria to consider when selecting a bolt:
1. Choosing the Right Bolt for the Application
Each bolt type is designed for a specific purpose. Different fastening elements are used in industries such as construction, automotive, aerospace, and marine. For example:
- Hex head bolts are commonly preferred in the construction industry.
- Brass bolts are used in the electrical and electronics industry.
- High-strength stainless steel bolts are preferred in the aerospace industry.
2. Material Type
The material of the bolt is an important factor in selection. The most commonly used materials include:
- Steel bolts: Ideal for general use and available in different strength grades.
- Stainless steel bolts: Resistant to water and moisture, suitable for outdoor use.
- Inox bolts: Highly corrosion-resistant, widely used in the food, chemical, and marine industries.
- Brass bolts: Preferred in electrical and electronic applications due to their high conductivity.
3. Bolt Size and Thread Type
For secure fastening, using the correct size bolt is essential. The most common sizes are based on metric and inch systems. Additionally, thread types are important:
- Fine-threaded bolts: More resistant to vibrations, commonly used in the automotive industry.
- Coarse-threaded bolts: Provide stronger connections, typically used in construction and heavy industry.
4. Surface Coating and Corrosion Resistance
To ensure durability, the surface coatings of bolts play a significant role. The following coatings protect bolts from environmental effects:
- Galvanized coating: Zinc coating enhances corrosion resistance.
- Cadmium coating: Used in the aerospace and marine industries.
- Stainless coating: Provides the highest corrosion resistance.
5. Bolt Strength
The strength of a bolt is directly related to the material from which it is made. Strength grades are usually marked on the bolt itself. For example:
- Grade 8.8 bolts: Medium strength, used in general assembly work.
- Grade 10.9 and 12.9 bolts: Preferred for heavy-duty industrial applications requiring high strength.
6. Compatibility with Fasteners
The bolt must be compatible with the nut, washer, and other fastening elements used with it. Mismatched parts can weaken the connection.
7. Torque Value and Tightening Process
Each bolt has a specified torque value. Over-tightening or under-tightening can compromise the safety of the connection. A torque wrench should be used to ensure the correct torque value.
8. Special Bolts for Specific Applications
Some industries require specially designed bolt types:
- Eye bolts: Used for lifting and suspension applications.
- Flanged bolts: Provide a larger surface area for a stronger grip.
- Countersunk head bolts: Ideal for applications requiring a flush and aesthetic finish.
Choosing the right bolt ensures a strong and durable connection. Factors such as material, thread type, coating, and strength grade should be carefully considered based on the application. Incorrect bolt selection can lead to loosening over time and cause serious failures. Therefore, the most suitable bolt type should be determined and applied with precision for each use case.
Key Considerations in Bolt Assembly
Bolt installation is a crucial process to ensure the safety and longevity of fastening elements. If the installation is not done correctly, issues such as loosening, deformation, or breakage may occur in the connections. Therefore, the torque value applied during installation, the tightening method, and the equipment used are of great importance.
First, surface cleanliness must be considered during bolt installation. The surface to be connected should be free of oil, dirt, or rust to ensure a secure tightening process. Additionally, other fastening elements used alongside the bolt, such as nuts and washers, should be compatible. Mismatched components can negatively affect the strength and durability of the installation.
The torque value applied during installation is also crucial. Each bolt type has a specified optimal tightening torque. Over-tightening can cause deformation or breakage of the fasteners, while under-tightening can lead to loosening and eventual failure of the connection. Therefore, precise tools such as torque wrenches should be used to ensure the correct tightening process. In applications requiring high strength, the tightening process should follow a specific sequence and be applied gradually.
Finally, after the bolt installation is completed, periodic inspections should be conducted. Over time, vibrations, temperature changes, and external factors can cause connections to loosen. Regular maintenance and inspections help maintain the integrity of bolt connections and identify potential issues in advance. By using proper installation techniques and maintenance practices, connections can be made durable and secure over the long term.
Applications of Bolts
Bolts are indispensable fasteners in modern engineering and industrial production. Over the years, technological advancements, manufacturing techniques, and material science developments have expanded and diversified the applications of bolts. Below, you will find the primary areas where bolts are used and detailed explanations of why they are preferred in each field.
1. Construction and Architectural Applications
The construction industry is one of the most critical sectors where safety and durability are paramount. Therefore, bolts used in structural connections stand out with their high strength and long lifespan.
- Steel Structures: The main skeletons of modern buildings and bridges are joined using steel fasteners. Bolts enhance the load-bearing capacity of structures and provide resistance against external factors such as earthquakes and wind.
- Roof and Facade Assembly: Bolts used in roofing systems and facade connections are resistant to weather conditions and provide a solid structure for many years.
- Prefabricated Structures: In prefabricated construction systems, bolts are preferred for their ease of assembly and quick installation.
2. Automotive Industry
The automotive industry is a field where high performance and safety are crucial. Many components of vehicles, such as the engine, chassis, and braking systems, are fastened using bolts.
- Engine and Chassis Connections: Bolts used in assembling engine parts and chassis elements are designed to withstand extreme heat and vibration.
- Braking Systems: Special bolts used in mounting brake calipers and discs directly impact vehicle safety.
- Suspension and Steering Systems: Bolts used in suspension elements and steering connections ensure secure fastening under dynamic loads.
3. Machinery and Industrial Equipment
In industrial production and machinery manufacturing, ensuring the secure assembly of each component is of great importance. Bolts are preferred in this field for their durability and precise assembly requirements.
- Manufacturing Machines: CNC machines, presses, and fabrication equipment in heavy industries use specially designed bolts that require high torque connections.
- Assembly Lines: In production lines, bolts used in fast and reliable assembly operations are compatible with automation systems.
- Robotic Systems: Special bolt types are used in robotic arms and industrial automation systems that require precise adjustments.
4. Electrical and Electronic Applications
- Assembly Panels: Bolts used in securing circuit boards, control panels, and other electronic components stand out due to their small size.
- Cabinet and Case Assemblies: Durable and compact fasteners are preferred in industrial computer cases and telecommunication equipment.
5. Aerospace Industry
- Aircraft Body and Wing Connections: Fasteners that ensure the structural integrity of aircraft require high strength and lightweight properties.
- Spacecraft: High-tech bolt systems are developed for connections exposed to extreme temperatures, radiation, and vacuum conditions in space.
- Engine and Propulsion Systems: Bolts used in aircraft engines and propulsion systems maintain their performance even under high speeds and extreme conditions.
6. Food and Pharmaceutical Industry
- Hygienic Assembly: Bolts used in food processing plants and pharmaceutical production lines are designed to withstand cleaning and sterilization processes.
- Chemical Resistance: In this field, bolts made from corrosion-resistant stainless materials ensure product safety.
7. Energy and Infrastructure Applications
- Electrical Stations: Durable and long-lasting bolts are used in high-voltage towers, transformer assemblies, and other critical infrastructure elements.
- Renewable Energy: In wind turbines and solar panel assemblies, corrosion-resistant fasteners that withstand external elements are preferred.
8. Other Special Applications
- Furniture and Decoration: In modern designs, aesthetically appealing fasteners are used to ensure both functionality and elegance.
- Agricultural and Machinery Equipment: Bolts play a critical role in continuously operating agricultural machinery and outdoor applications, ensuring durability and longevity.
The sectors mentioned above demonstrate how extensively bolts are used. The types of bolts used in each sector are selected according to specific requirements and are designed in compliance with quality standards during the manufacturing process.
Bolt Manufacturing
Bolt manufacturing is a process that requires high precision and the use of quality materials. During production, raw materials such as steel, stainless steel, or brass are commonly used. These materials offer different properties in terms of durability and corrosion resistance. In the initial stage, steel rods are cut to specific lengths and shaped at high temperatures to form bolts. This process can be carried out using hot forging or cold forging methods.
After the shaping process, the threading phase of the bolts begins. Threads can be created using rolling or cutting methods. The rolling method enhances the material’s durability, providing stronger connections. Next, surface treatments are applied to enhance the bolts’ resistance to corrosion. Coating methods such as galvanization, phosphating, or zinc plating are selected based on the intended application. Finally, quality control tests are conducted to ensure each bolt meets specific standards.
To learn more about one of our manufacturing processes, DIN 444 Eye Bolt Manufacturing, you can watch the video on our YouTube channel. In this video, you can examine the production stages of eye bolts in detail and see how fastening elements are manufactured. Keep in mind that the correct manufacturing process plays a crucial role in ensuring high-quality and reliable fastening elements.
Discover the most suitable bolt types for durable and secure connections, and get detailed information: contact us